When we talk about prestressed concrete, the things that we are mostly concerned about are the compressive strength gain with respect to time, and the prestressing tendon relaxation with respect to time. Figure 1 shows various time-dependent effects for concrete including creep and shrinkage.
The factors that affect the creep rate include water/cement ratio, age and strength of the concrete when it is subjected to stress, and ambient temperature and humidity. Creep rate also depends on many other factors related to the quality of the concrete and conditions of exposure such as the type, amount, and maximum size of aggregate; type of cement; amount of cement paste; size and shape of the concrete mass; amount of steel reinforcement; and curing conditions (Robert Salca, tech support, midas UK).
For shrinkage, its rate decreases much faster with time compared with creep as shown in figure 1. Finer aggregates and finer gels result in increased shrinkage, the moisture content of the concrete and the relative humidity of the ambient medium have a big influence on carbonation shrinkage, and harder aggregates with higher modulus of elasticity decrease shrinkage.
Do you need to perform construction stage analysis for time-dependent materials?
There are cases where you cannot calculate the losses directly for PSC. According to AASHTO section 5.9.3.5 shown in figure 2, for staged construction or multi-staging prestressing, you should use a time-step method, hence construction stage analysis in midas Civil.
According to AASHTO article C5.9.3.5, staged construction refers to any bridge whose structural statical scheme undergoes changes before reaching construction completion. An example would be segmental balanced cantilever construction where adjacent cantilevers are joined to make a new, continuous structure. Staged construction can also refer to changes in the cross section of superstructure members through composite action, where prestressing is stressed both on the non-composite and then composite cross sections. An example would be spliced girder construction, with prestressing stressed in a first stage to make the girders continuous, and then in a second stage after the casting of the deck slab.
Construction stage analysis in midas Civil
Midas uses stages to control construction sequences. The software activate or deactivate structural members, loads, and boundary conditions, or all three, at any given stage. Each stage is relative to time, which can be input in terms of number of days. For the time-dependent material in construction stage analysis, linear analyses can be performed in midas Civil to simulate the effects of creep, shrinkage, compressive strength gain, and prestressing tendon relaxation. Figure 3 shows a construction stage model where segments of prestressed beams were built in sections that need to be analyzed using construction stage analysis.
The general procedure to define construction stage analysis with time-dependent material in midas Civil can be summarized below:
-
-
-
-
-
-
-
Create model: geometry, material, sections, load, boundary conditions
-
Set up groups to be used for activation / deactivation in construction stage analysis
-
Define time-dependent material properties
-
Link the time-dependent material properties to the applicable material
-
Create the stages and control options
-
-
-
-
-
-
To define the time-dependent material, you need to define the type of curves that defines creep, shrinkage, and compressive strength gain with respect to time. There are various models that can be used, and as shown in figure 4, AASHTO allows the usage of any of the material data available in the resources below.
The material models highlighted above are built in as data base in midas Civil directly, where you can select FIP or AIC codes, etc. You are able to define your own material as well besides using the built in material models. If you are experiencing a large amount of creep and shrinkage strain, you can cross check by looking at what the predicted forces are from other models. Comparing the structural behavior of your time-dependent material model that has unexpectedly large creep and shrinkage with the that of other models will also help you understand the differences.
Other than time-dependent materials, sometimes there are confusions on what load cases are and how to use them in load combinations. The most unique thing that midas Civil does is that the software separates out a specific load case in a construction stage model, which is called erection load case in the software. It enables you to define a load case that you do not wish to be included in the dead load, and is commonly used for wearing surface where you can apply a different load factor other than dead load factor. It is very useful because the separation of load cases allows you to control them individually. Besides that, if you have something that is applied during the construction process as a load, but do not want it to be considered during the final dead load calculation, you can set it up as an erection load. In other words, erection load case can be a temporary load case or a construction load case.
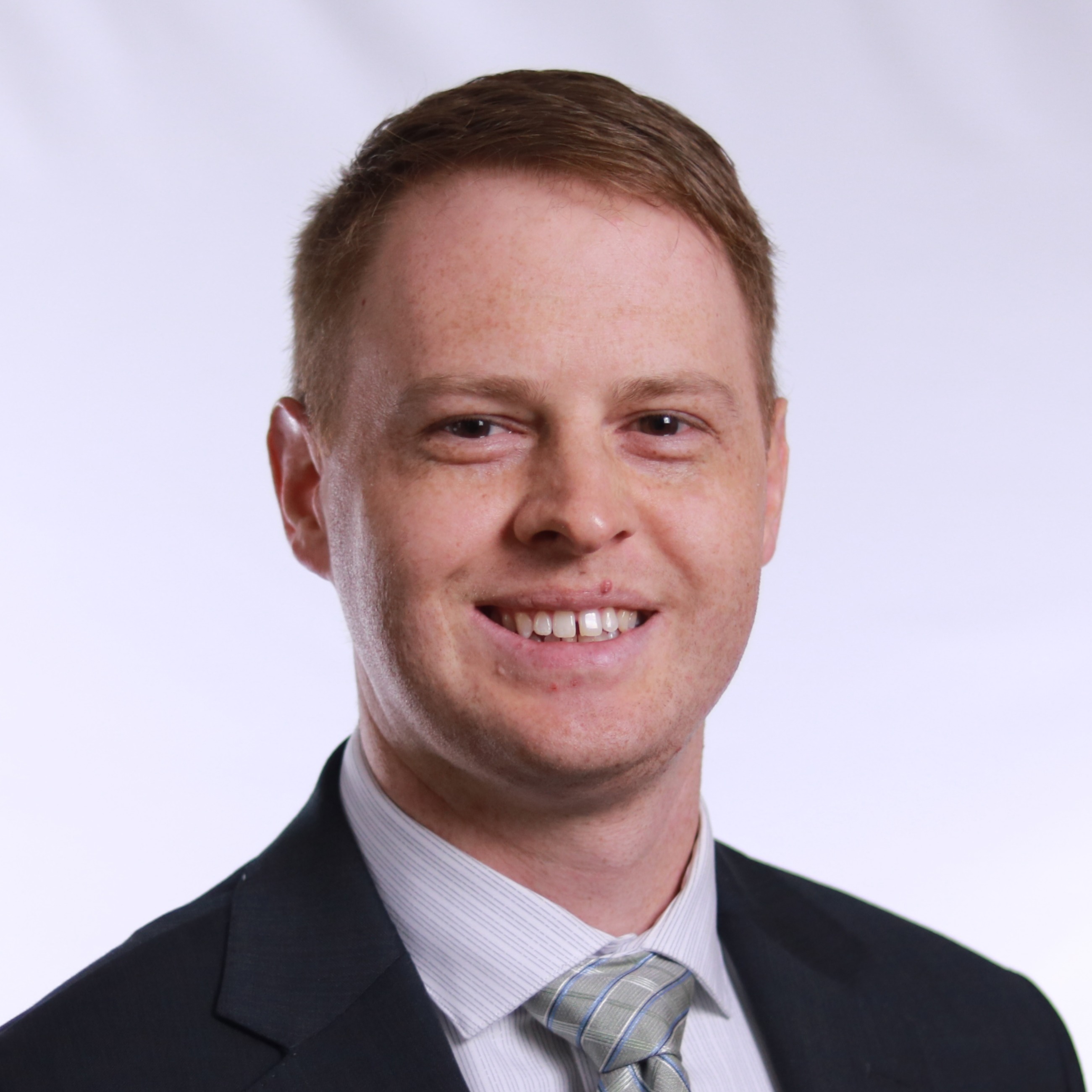
He is a very experienced engineer with more than ten years of experience. He was a Lead Structural Engineer at Puget Sound Naval Shipyard for more than six years. He joined the CH2CM bridge group in 2015 and has worked on bridge engineering, load rating, and project management. He is currently the Structural Engineering & Architectural Group Lead in the Corvallis, OR office.