Complex Load Rating for Steel Bridges
Michael Baker engineers share their overall load rating procedure for complex projects and insight into other "girder bridge" challenges for unbraced sections. A sample bridge and project case study is used to demonstrate their workflow and subsequent results.
First Step
Bridge Rating Factor can be simply stated as a measure of safety of a bridge for a specific loading. The general rule of thumb is to begin as simple as possible with approximate analysis or a line girder approach and check if the line girder rating factor is greater than 1. Then the bridge is at an adequate level of safety, requiring no additional work. However, if the rating factor is found to be less than 1, the engineer has to make a decision: 1) Rehabilitate or strengthen the bridge to improve capacity. 2) Update the bridge parameters to reduce the live load demand. 3) Perform a refined analysis to get a better demand.
Choosing the Right Model Type
Why the emphasis on the modeling? It's because the model type directly affects the bending stresses, forces, and displacements meaning differences of live loads used for the rating factor. Assuming the engineer determined the adequacy of refined approach and determined the requirement of 2D or 3D (from AASHTO LRFD 4.6.1.2.4b); they would check the NCHRP Report 725, in the case of curved and skewed steel bridges. NCHRP Report 725 provides a recommendation for design and construction and also for analysis, making it applicable for load rating; therefore giving types of modeling approaches as well. As a verification of the validity of the recommendation, Michael Baker sampled and compared the Minnesota Bridge 27W02.
What's the Difference
As per NCHRP Report 725, a 2D grid and 1D line girder analysis would adequately compute the major axis bending stress, vertical displacement, and girder layover. However, the 2D grid and 1D line girder analysis would be highly inaccurate for cross-frame forces and flange lateral bending stresses. For this reason, the recommendation was to utilize a refined model for the Minnesota Bridge 27W02. The results concluding NCHRP Report 725 to be accurate.
Finishing the Workflow
Once the model is complete, following the load rating procedure yielded the rating factors through a combination of Excel spreadsheets and Civil outputs.
"Using no more than a spreadsheet on your end, but with powerful 3D FEA information in the background, overload permits for suspension, cable-stay, arch, truss, rigid frame, and other complex bridge types can be processed in less than a minute for many complex structures."
-Francesco Russo
Products Used: midas Civil
midas Civil is an engineering software for the design of bridges and civil structures. It features a distinctively user friendly interface and optimal design solution functions that can account for construction stages and time dependent properties. Its highly developed modeling and analysis functions enable engineers to overcome common challenges and inefficiencies of finite element analysis.
ROI:
-
midas Civil allows the full control of modeling the bridge, especially the cross frames.
-
AASHTOWare BrR is unable to handle the rating for steel bridges with irregular geometry.
-
midas Civil's load tracer allow to design the static case for the concurrent force outputs for multiple cases.
-
AASHTO LRFD bending, sheer & torsional strength, member forces & stresses for each construction stage, and max & min stress summation output checking.
-
Automatic generation of load combinations all in MS Excel format calculation reports.
Watch Part 1 and Part 2 of the Load Rating Series Here:
/Daniel%20Baxter%20346_240.png)
Daniel Baxter is a bridge department manager in Michael Baker's Minneapolis office, where he also serves as a project manager and senior bridge engineer. He has been involved in both the rehabilitation, design, and load rating of many complex bridges such as the Third Avenue Bridge, Winona Bridge, High Bridge, Franklin Avenue Bridge, Lafayette Bridge and Hastings Bridge, all over the Mississippi River. He also recently led the analysis of 18 existing pier caps with sectional and strut-and-tie methods and helped develop procedures for the design of 38 new pier caps using the strut-and-tie method. He also serves as an NHI-certified instructor for multiple NHI bridge design and load rating training courses, including Strut-and-Tie Modeling for Concrete Structures. He is highly experienced in complex finite element analysis, has given eight presentations at the International Bridge Conference, and has published several papers in peer-reviewed journals. He graduated with a B.A. in Physics from Carleton College in 2001 and received a B.S. in Civil Engineering and an M.S. in structural engineering in December 2003 from Washington University in St. Louis. He is a licensed professional engineer in Minnesota and a licensed structural engineer in the state of Illinois.
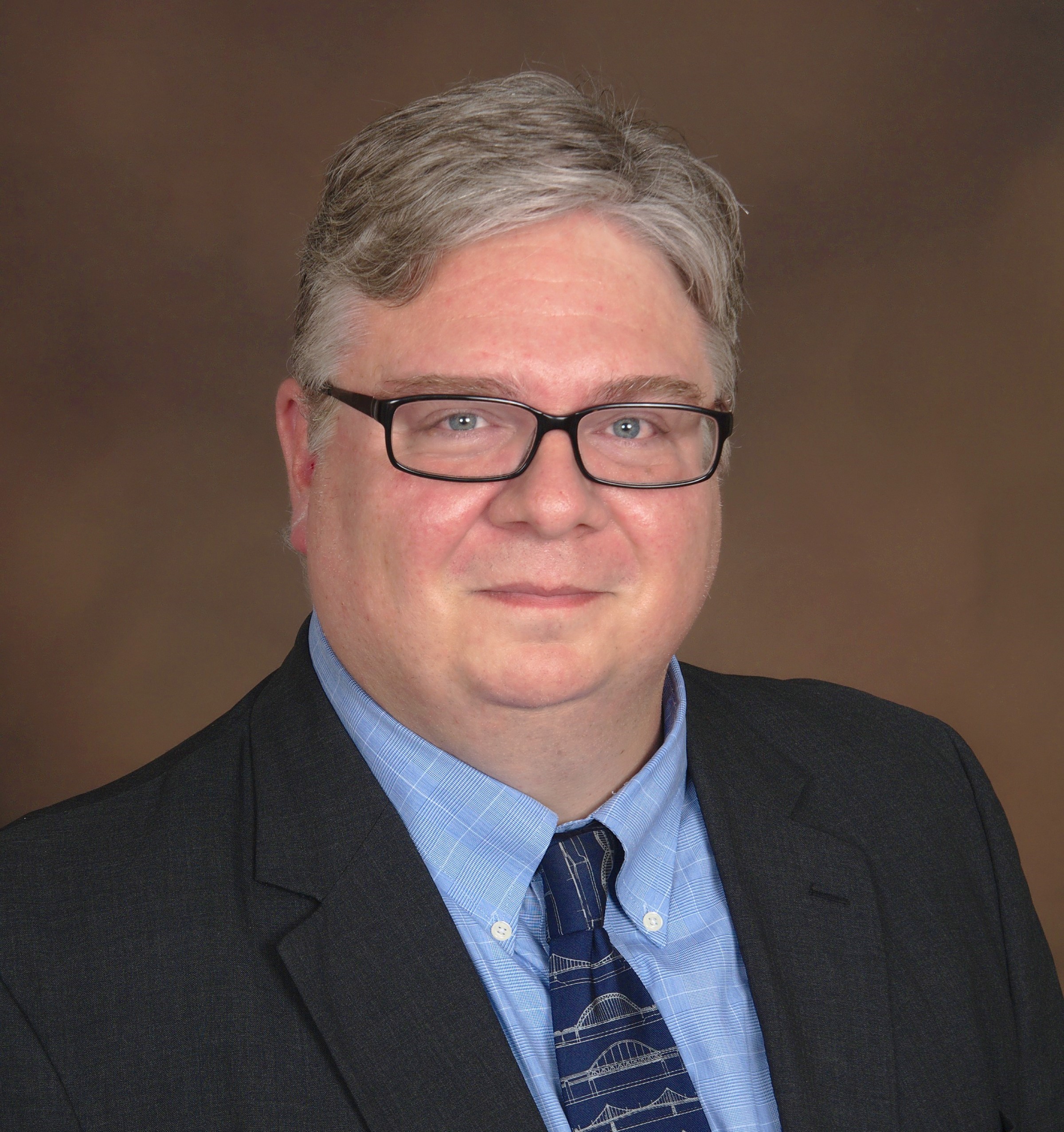
Francesco Russo is the founder and principal of Russo Structural Services, with a career spanning more than 25 years in structural engineering, specializing in complex bridge analysis and design. His extensive experience includes roles such as Vice President & National Technical Director of Bridge Engineering at Michael Baker International and positions at HNTB Corporation and URS Corporation. With a PhD in Civil Engineering from Iowa State University and an MS from Temple University, Russo has a solid academic background complementing his professional expertise. His journey began as a Special Projects Engineer at the Iowa DOT Office of Bridges and Structures, laying the foundation for a career marked by continual challenges and diverse roles. Known for his teaching abilities in both academic and professional settings, Russo has also made significant contributions to forensic engineering and expert witness report preparation. His skills encompass a wide range of areas including structural analysis, finite element analysis, construction management, and proposal writing, positioning him as a proven expert in bridge engineering and a recognized lecturer in LRFD engineering.